- TOP
- Cutting-edge Research and Social Contribution
- Cutting-edge Research
- The unique structure of "nanoporous metals": Key to developing innovative catalyst materials
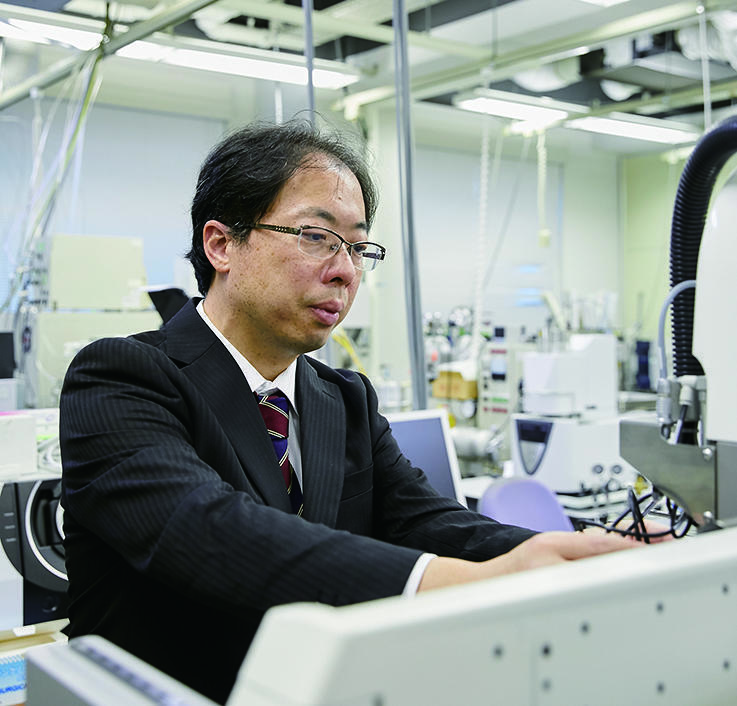
The unique structure of "nanoporous metals": Key to developing innovative catalyst materials
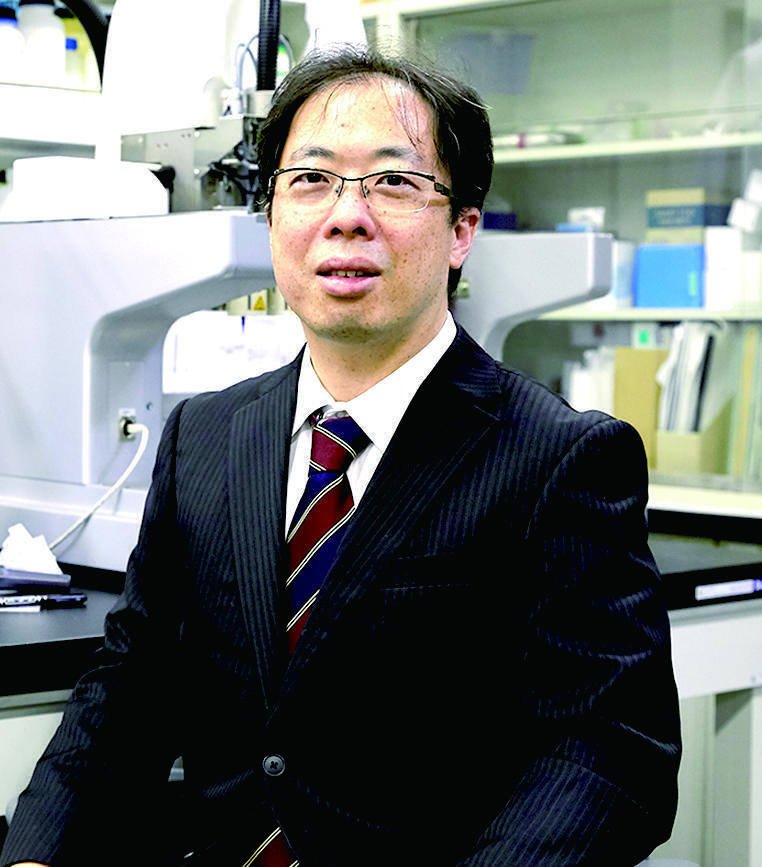
Development of nanoporous catalysts to reduce environmental impact
In developing the concept of "dealloying," a technique for producing nanoporous metals, Prof. Fujita and his collaborators were inspired by the phenomenon whereby specific elements selectively elute from an alloy due to corrosion. The technique is very simple and involves simply alloying metals that are stable and metals that are unstable to corrosion, and then performing selective corrosion with an electrolytic solution. Prof. Fujita: "No special experimental equipment is needed to fabricate nanoporous metals through dealloying, so the technique is very simple and has great potential."
Among the diverse functions of nanoporous metals, catalyst applications are particularly promising. In previous nanoparticle catalysts, multiple nanoparticle metals were arranged on the surface of an oxide. Only the vicinity of the nanoparticle was active, and other regions were not effectively used. A nanoporous catalyst, on the other hand, has a structure in which metal is complexly entangled with oxides, and thus not only does the active region greatly expand, the active time of the chemical reaction can be maintained for a long time because it has high durability.
Prof. Fujita has also begun developing a revolutionary new catalyst system which allows DRM to be driven at room temperature by a high voltage applied to the nanoporous catalyst (a conductor) and causing corona discharge*2. One recent trend is to optimize chemical reactions for industrial purposes by leveraging external fields, such as light or an electric field, as the driving force to control the reaction path and speed. With conventional nanoparticle catalysts, however, the reaction only proceeds near the nanoparticles dispersed on the surface of an oxide, so extremely low coupling efficiency between the catalyst and external field is an issue. To solve this problem, Prof. Fujita and colleagues turned to nanoporous catalysts because they can accumulate electric fields on their surface. The idea was to bring the electric field of the catalyst surface closer to the gas which generates the external field through corona discharge, thereby improving the coupling efficiency with the external field, and activating the catalytic reaction. Experiments with the developed equipment confirmed that the catalyst accelerates the reaction through corona discharge.
Other innovative results have been accomplished, promising substantial reductions in environmental impact. One notable achievement involves applying acid etching and heat treatment to impart electrical conductivity to a metal-organic framework (MOF) initially impermeable to electricity. This transformation successfully converts it into an exceptional catalyst for water electrolysis.
*2) Phenomenon which occurs due to the non-uniform electric field when a high voltage is applied to a local point like a sharp electrode
Striving for a "universal catalyst"
Another major theme Prof. Fujita is exploring is the development of "super multi-element catalysts" combining multiple elements.
Behind this success was an idea based on "reversal." A bottom-up technique was used to make previous multi-element catalysts, building up elements one by one. Prof. Fujita and his colleagues had the opposite idea. They used a "top-down" technique of first fabricating a composite alloy of multiple elements and then optimizing the end product by removing those that are unneeded. This overturned the received wisdom regarding catalyst design techniques, and led to dramatic progress.
The final objective of Prof. Fujita's research in this area is a universal catalyst that works in all reactions.
The method of choosing elements is also important for fabricating multi-element catalysts. On that front, Prof. Fujita is planning to merge catalyst science and data science, and develop a system for finding optimal combinations of elements. In March 2021, the university installed a state-of-the-art electron microscope equipped with outstanding features like high resolution and wide-ranging analytic capabilities. "This equipment will likely drive a quantum leap in the progress of our research," says Prof. Fujita with conviction.
Date of posting: February, 2024